In the last month the Pentagon Plastics Group – Phoenix Engineering and Pentagon Plastics Ltd – saw delivery of a major new investment in an ALT 500 Laser Welder.
Located in the Phoenix Engineering factory, the new addition joins an extensive set-up of plant machinery. The TLM laser package cost £130,000, with the bulk of the investment from Phoenix Engineering; it’s a huge, self-funded statement of intent to offer state of the art internal and sub-contract work.
The purchase included, but is not limited to, the ALT 500 Laser Welder, AL300, tilt-able turntable, magnetic clamping, integrated extraction and laser wire feed system.
Improved services
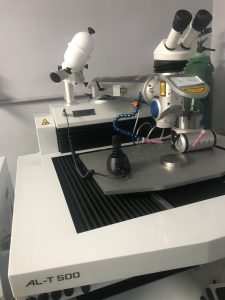
Installed on 17th November 2017, the Phoenix Engineering team will have three fully trained operatives to complete highly skilled laser welding projects on a daily basis. This will ensure internal and sub-contract support work can meet demand.
The investment follows laser welding being recognised as a major sub-contracting expense across the Group over several years. Through investments in the right machinery, such as the ALT 500, the Group will be able to provide reduced lead times for tooling work, an improved workflow and a new business service to offer new and existing clients.
Growth for Phoenix
Since Phoenix Engineering was acquired by Pentagon Plastics in 2016, it has gone from strength to strength, which is fantastic to see for such a long standing business first founded in 1955.
Paul Edwards, MD of the Pentagon Plastics Group recognises this investment as a major step forward for Phoenix Engineering, stating, “It’s a testament to all of the hard work from our staff who work tirelessly to review and improve the services we offer.’’
The laser welder will enable us to increase turnover, improve process efficiency and generate more profit to reinvest in our services, which is positive news for our customers and will help us support local businesses.”
Tooling Manager at Phoenix Engineering, John Horspool, says, “At Phoenix the majority of tooling demand is for caps and closures, ranging from 4 to 64 impressions and expediting servicing and repair are key to keeping the tool downtime to a minimum.
Many of the elements require laser welding to reinstate shutoffs etc., therefore the weld needs to be very exact and repeatable, driving the business need for a high spec machine, with a rotary axis, self-feed wire and programmable movement in all axes.”
For more information on all the services we offer, please contact the team on 01403 264 397.