With all the design technology now at our fingertips it is easy to design anything that the mind can imagine, but can you make it?
As a UK based plastic injection moulder supplying into a range of industry sectors, we have seen all manner of product designs over the years. With the advances in cad modelling and 3D printing product designs that we receive are usually of good calibre from a functional point of view with due consideration given to how the product will perform. However, we often find that parts are designed more in line with machining rather than injection moulding which are two quite different techniques.
Here at Pentagon the first stage of any new enquiry is what we call a DFM, this is a basic product review looking at the part from a Design for Manufacture perspective.
Once we are past the initial enquiry stage and a customer is looking to work with us at Pentagon on a new project a full Design for Manufacture review is undertaken by one of our technical team.
The full DFM review encompasses the following elements:
1. Mouldability– to ensure all features can be produced as a moulded part
2. Undercuts – access whether any features will prevent a conventional open/shut tool
3. Drafting– check suitable draft is applied to suit surface texture and tool function
4. Aesthetics– access whether any features will cause visual imperfections when moulded
5. Process Flow Analysis – support software to identify any process issues or concerns.
Once we have reviewed the product(s) our experts will collate a report for the customer highlighting any potential design issues that need to be considered, recommendation to aid the moulding process and any potentially cost saving opportunities.
Our recommendations may include (but are not limited to)material selection, shut-off areas, feed points, drafting, surface finish and maintaining even wall sections. These suggestions can potentially provide customers with cost savings on initial tooling as well as ongoing production and the opportunity to optimise the process often providing a higher quality finished product.
It is imperative that a product designer fully understands the manufacturing process that they are designing products for. Having a detailed and informed understanding of the process by which a product will be made will ensure that there is minimal time in getting the part to production as every consideration will have been given to the manufacturing stage at initial design.
There are of course cases where a design change is not possible,and we support customers in these circumstances and offer our best technical support and advice to find a solution. However,we do find that our customers are pleased with the offerings of the DFM’s giving them confidence that we are a supportive business and not just ‘in it for the sale’. We recognise that mould tooling is a huge investment which is why we are committed to helping our customers get their product lines off the ground and ensuring continued success in production.
Here at Pentagon we pride ourselves on the level of technical support that we provide our customers in relation to both mould tool manufacture and repeat production performance.
Laying firm foundations at the initial design stage will enable your project to be quoted accurately for your manufacturing process of choice, enable your product to come to market in a timely manner and allow you to see a faster return on the investment in tooling costs.
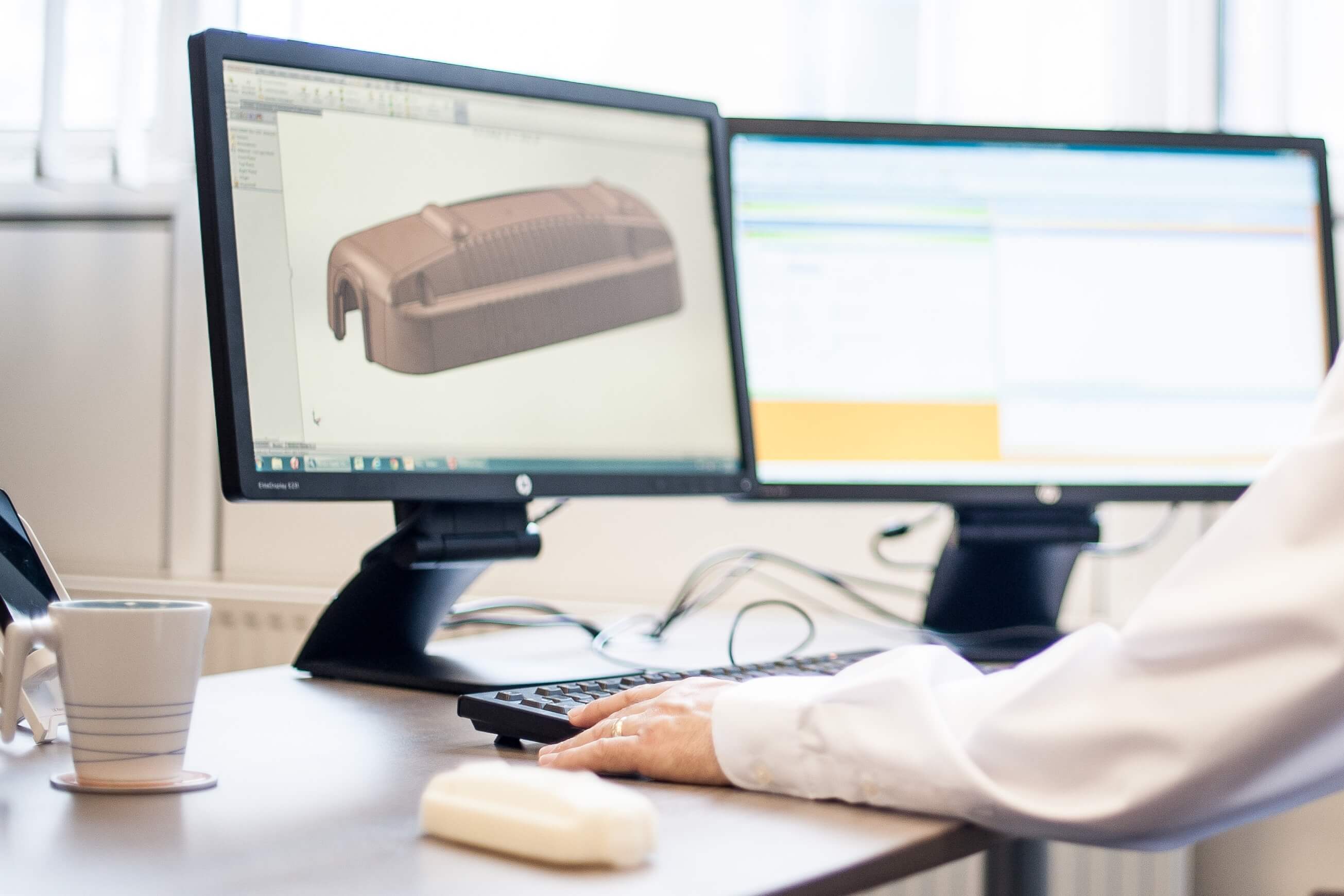