Although plastic injection moulding and CNC machining may seem similar, operate on profoundly different principles. The two processes provide different applications for a range of industries from consumer products to medical tools. Here, we’ll delve into the intricacies of these two manufacturing methods and discuss their differences.
What is Injection Moulding?
Injection moulding is a manufacturing method used for producing plastic parts and components. Raw thermoplastic material is melted and injected into a mould to create a product. Plastic injection moulding is used to create a wide variety of parts, such as:
- Household items: light switches, bottle caps, kitchenware, toilet seats etc.
- Consumer goods: toys, storage containers, phone cases etc.
- Medical devices: sterile syringes, medication trays, surgical equipment etc.
- Automotive parts: cup holders, gear parts, dashboards etc.
- Electronics: casings, buttons, switches etc.
Plastic injection moulding can create large volumes of parts quickly and efficiently.
What is CNC Machining?
CNC (Computer Numerical Control) machining is the process of pre-programming computer software to dictate the movement of factory tools and machinery. It essentially means cutting complex shapes from a block of material that would have otherwise been impossible to achieve manually. CNC machining is used to create a range of products, such as:
- Art
- Jewellery
- Candle holders
- Coasters
- Board games
- Décor
- Prototype parts
- Architecture models
CNC machining can cut metal, plastic, wood, foam, or almost any other material.
Advantages of Injection Moulding
Plastic injection moulding is known for its efficiency in producing high-volume parts and delivers numerous advantages.
Efficiency in Producing High Volume of Parts
Plastic injection moulding is unrivalled in its ability to produce repeatably large quantities of parts within a short timeframe. Once the mould is made and set in the press, the process runs smoothly with no or little human intervention. This makes it an excellent choice for cost-effective mass production.
Ability to Create Complex Parts
Injection moulding allows you to create the most intricate geometries and designs that would otherwise be challenging or impossible with CNC machining. This process allows for detailed and precise mould designs and enables the creation of features like undercuts, threads, and thin walls.
Consistency
Because of the accuracy of injection moulding, it facilitates the creation of high-quality, precise products repeatedly that are consistent in quality and appearance. The precision of the injection moulding process ensures each part is identical.
Reduced Labour Costs
The automation used in injection moulding can remove the need for additional labour, making it a great solution for lowering production costs. Once the machines are set up and calibrated, they can operate with minimal supervision.
Material Efficiency
This process minimises waste as excess material can be recycled. This makes it a sustainable choice for manufacturing.
Advantages of CNC Machining
CNC machining is known for its precision and flexibility and it stands out in its ability to adhere to complex designs. Here are just some of the advantages this manufacturing process offers:
Precision
CNC machines are great in demanding scenarios where high precision is essential. This process can produce parts with tight tolerances and complex geometries with ease. This process is ideal for applications demanding high accuracy and consistency.
Material Versatility
CNC Machining can work with a diverse range of materials from rigid materials like metals to flexible plastics. This offers a broad range of applications for many industries. This adaptability makes it perfect for industries where different materials are needed.
Design Flexibility
CNC machining allows for quick design changes at most points in the process without significant additional costs. This is because it is a computer programme that determines the design rather than a mould.
High-Quality Surface Finish
CNC machine parts require minimal post-processing. This ensures a high-quality finish that is critical in certain industries like medical or aerospace.
Comparisons of Plastic Injection Moulding vs CNC Machining
Cost
Whilst CNC machining has a significantly lower upfront cost compared to injection moulding, injection moulding becomes cost-effective at high production volumes due to the mould’s cost being spread over many parts.
Speed
CNC machining is ideal for small-volume runs due to its quick setup, while injection moulding is better for large-scale production where multiple cavity moulds can quickly produce parts. CNC machining is faster, whereas plastic injection moulding takes time to produce the mould.
Volume
If you have a large-print run, injection moulding outperforms CNC machining every time. It can produce multiple parts simultaneously with multi-cavity moulds while CNC machining can only produce parts one by one.
Materials
CNC machining offers greater material versatility as you can work with a wide range of metals, plastics, and wood. Injection moulding is only suited to thermoplastics which may be too soft for CNC machining. There are however endless choices of thermoplastic materials with varying properties now available that are compatible with the moulding process.
Tolerances
Injection moulding can achieve tolerances within ±0.500 mm (±0.020 inches) suitable for many applications. For superior precision, CNC machining offers tolerances as tight as ±0.500 mm (±0.020 inches).
Environmental
Injection moulding produces minimal waste as excess material is often recyclable. CNC machining generates more waste, but recycling initiatives can reduce its environmental impact.
Choose Pentagon Plastics for Plastic Injection Moulding
In summary, both injection moulding and CNC machining offer unique benefits. CNC machining offers precision and flexibility whereas injection moulding excels in high-volume production, environmental impact and creating parts with uniform properties.
If you’re looking to take the next step in your manufacturing journey, don’t hesitate to reach out. Our team is here to help you optimise your production strategy to achieve high-quality results.
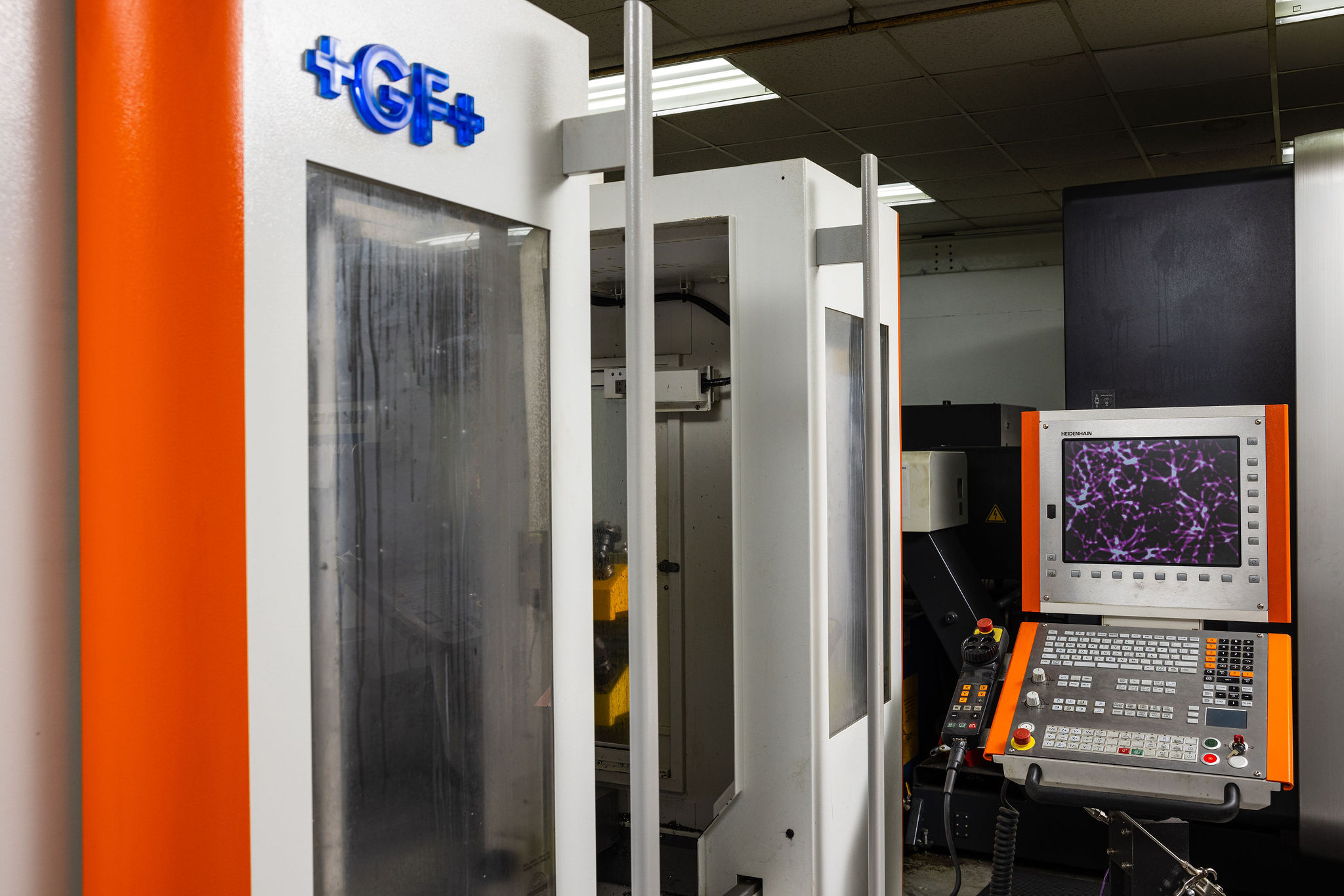